A prominent milking equipment dealer in Idaho’s Magic Valley near Twin Falls recently converted a former tractor dealership and equipment repair shop into its own hub for technology research and development. That company – Automated Dairy – has been in operation for 35 years and employs more than 150 workers in seven dealerships throughout Idaho, California and Nevada.
The company’s latest innovation is an automated teat preparation system called TURBOSPRAY. The product has been on the market for 18 months, yet over 200 systems have been installed across 85 dairies. The success of this latest innovation is hopefully one of just many more to come, says the team of engineers in the research and development department.
“The main goal for the Innovation Center is obviously to innovate,” says Ben Gines, the company’s engineering manager. “We’re looking for innovation trends and what innovations every dairy needs.”
Gines and the engineering team receive requests from sales reps related to their current dairy clients’ needs. They are then tasked with engineering solutions to these challenges when a suitable solution doesn’t exist. TURBOSPRAY was one such opportunity.
Dairies didn’t like the moving parts of many of the other teat spray wands or robotic milking prep arms, says sales manager Bryan Brown. They wanted something that was simpler to use and had fewer chances to break down.
What the team came up with was a walkover, air-assisted teat preparation system to apply teat spray prior to a cow entering or exiting the parlor. The system makes it possible for a dairy to eliminate at least one parlor employee (and sometimes two) who would otherwise have to manually apply teat dip to a cow as part of the pre-milking (or post-milking) procedure.
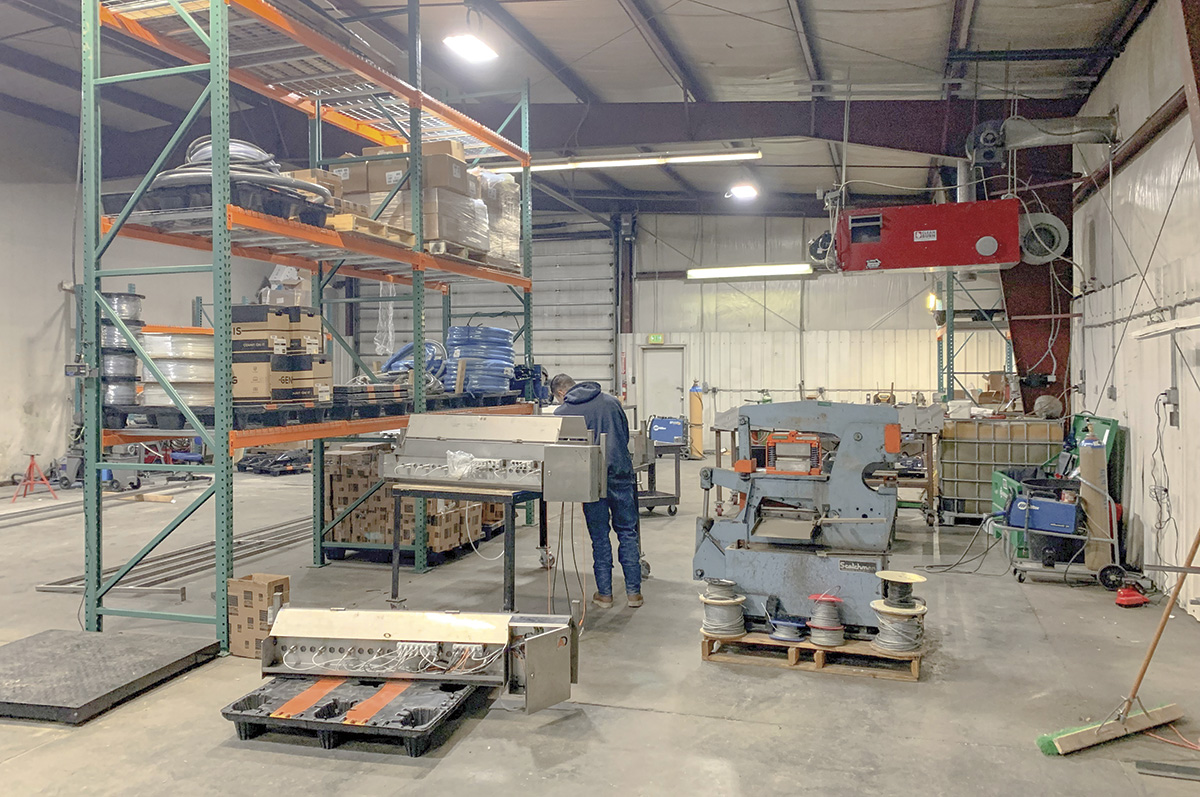
The TURBOSPRAY platform is mounted to the floor of a parlor entry (and/or exit) lane. The system uses a sophisticated set of sensors that tracks each individual cow and precisely sprays her as she enters and/or exits the milk parlor. The device is triggered to deliver a burst of teat spray at an ever-so-slight delay, so it is applied perfectly to the udder of the cow. The unit is installed far enough away from the entry to the parlor so the applied solution has had sufficient time to disinfect teats by the time the cow loads for milking. That means the time from loading to unit-on time is shorter with TURBOSPRAY, and most dairies quickly grasp that they can then milk more cows with the same parlor they already have.
To see it all in action, it almost looks too simple.
Research and development engineer Logan Kinghorn recalls the time when a dairy producer saw the TURBOSPRAY unit in action for the first time. The dairy producer said: “Why didn’t someone think of this before? It’s so simple.”
While it looks easy once perfected, Kinghorn knows there’s much more to it than just lasers, a puff of air and teat dip magically applied. He and the center’s team of engineers have spent months perfecting nozzle sizes, spray angles, air pressures and laser placements to deliver the ideal spray pattern – and be able to get it right where it needs to go regardless of whether a cow stops halfway through the unit or walks over it routinely.
“It’s always awesome when you show a dairyman your innovation and they say, ‘There’s nothing to this. I could make one in the garage,’” Kinghorn says. “You almost want to be insulted. But then you’re like, ‘Go for it.’ When they say something like that, we know we are doing something right.”
Although the research and development department has its own building and manufacturing shop now, it really started more than a decade ago when Automated Dairy designed a PLC-controlled automated milking equipment wash system. That innovation (now known as DairyLink) has now been installed on more than 200 dairies.
Working on that product helped the company see there are many more automation needs on a dairy than just the equipment wash system.
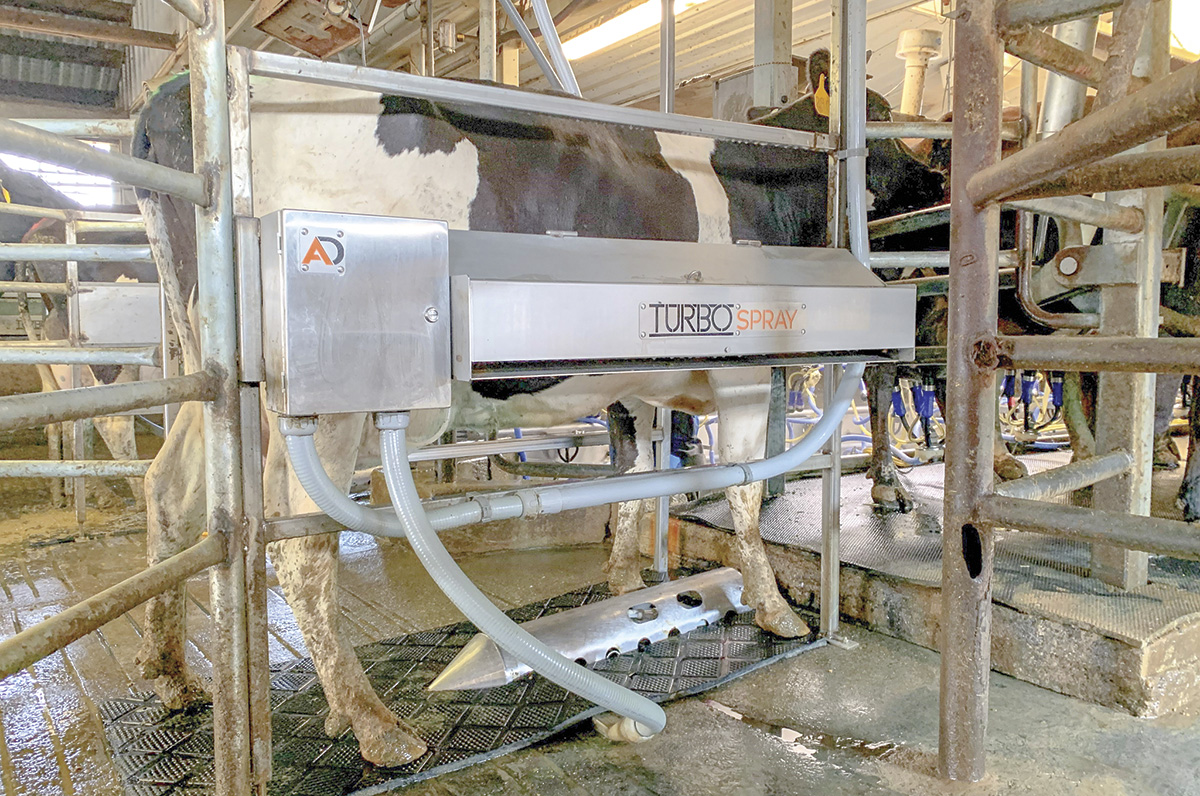
“We’re leveraging the deep history of the chemical side of our business to find new ways we can offer a dairy new, innovative solutions,” Gines says.
The team says that once you explain how a dairy could automate at least one part of their business – like an equipment wash or teat spraying – other ideas naturally start to flow.
“If you are walking around with a dairy owner long enough, you’ll end up with 10 different things they might see that would really make their life easier to have controlled,” Gines says.
Ideas that rise to the top of the development list are ones that can provide a reliable solution with a cost that requires no more than a six-month payback to the dairy.
“There’s a lot of products out there that the return on investment is a couple of years out,” Kinghorn says. “These days, it’s hard for a dairy to be able to predict what’s going to happen a couple years out, but more than likely they know what’s going to be going on in six months … It’s a lot easier for that dairyman to bite off on an innovation with a six-month payback.”
“Are we necessarily building the rotary or the parlor? No, that’s not really where we’re headed, but we have had a lot of customers that have approached us about controlling more of the parlor and aspects of their dairy,” Gines says.
To read more articles like this about advancements in ag tech for cows, subscribe to the author’s online publication The Cow Tech Report at Cow Tech Report.