Freestall barns are constructed to provide cows with shelter from winter winds and summer solar radiation. But beyond that, for cows to meet their genetic production potentials and for farms to maximize profitability, cow comfort is of utmost importance.
With well-designed and managed freestalls, we have measured lying times for up to 14.33 hours per cow per day for a large group of cows, but that also means cows are on their feet for the balance of the day.
Many times cows stand/walk on concrete alleys for an entire lactation – or possibly even all of their lives. It is therefore important to pay close attention to flooring and how it affects cows.
Observation and experience has shown the final finish on barn floors and alleyways is often the biggest oversight made when constructing a new barn and many times results in environmental lameness.
The relationship between environmental factors and lameness has been investigated by many individuals. Specific to flooring surfaces, research studies found that:
- Poor concrete surfaces and low freestall utilization caused a high incidence of sole ulcer and white-line disease in herds fed low levels of concentrates.
- Hooves of cows confined on new abrasive concrete wore 35 percent more than control cows housed on dirt.
- Hooves of all cows confined on a new concrete surface that had no special surface preparation wore more than they grew for the first two months after exposure.
Added to the above list are field observations that reveal improperly finished concrete floors will speed foot wear significantly enough to cause excessive culling due to lameness in the first three weeks of new barn occupancy.
Floors must provide confident footing for the cow and caretaker, with minimal foot and leg problems for the cow. Floors also must be economically affordable and durable.
There are two floors cows walk on: those already in place and those that will be constructed as part of a capital construction project. For both, specifics help ensure they are as adequate as possible.
Flooring and cows
By far, the most prevalent flooring surface in new and older barns alike is cast-in-place concrete. Concrete is an attractive flooring material to the dairy producer because it is readily available, durable, comparatively economical, relatively easy to place as it conforms well to irregular areas and can be finished in various ways to provide some level of traction.
At a minimum, floors for dairy cattle need to provide a flat surface that uniformly supports cows’ weight. This way, even pressure is exerted over the entire bearing surface of a cow’s hoof. Additionally, floors must provide confident footing for the cow, so she can navigate around the barn without worrying about slipping and possibly going down.
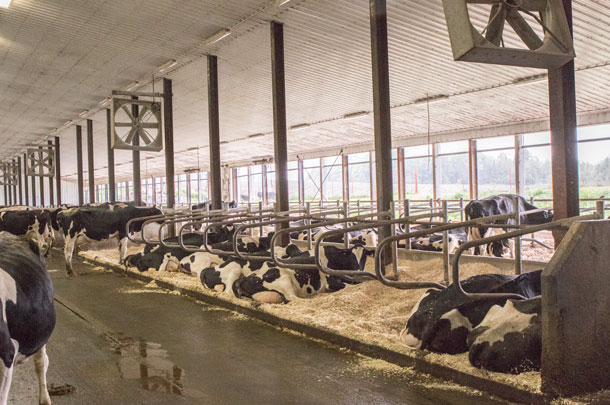
Concrete flooring by the stalls. Staff photo.
For this requirement, the approaches used boil down to two schools of thought. The first is to provide a textured surface that provides purchase for the cow’s foot before slip takes place. The second is to provide a means of catching a hoof digit before slippage becomes excessive and a cow goes down. The latter is sometimes referred to as the “slip and grip” practice.
Textured surface
Floors that are excessively textured in an attempt to eliminate slippage can wear hooves excessively, and smooth floors do not offer sufficient traction. There is a fine line between a concrete floor surface that is too rough and causes injury from abrasion and one that is too smooth and causes injury from inadequate footing.
Textured surfaces can be installed in freshly placed concrete using a bull float that has grooves cast or machined into one side of the float. If this method is employed, timing is critical, since concrete that is too wet will not maintain the groove formed by the float, and concrete that is too dry will not accept the groove at all.
A key to floor longevity is to specify a concrete mix design similar to what is used for applications requiring high-strength concrete (4,500 psi or more), use a water-to-cement ratio that results in a concrete slump of 4 inches or less, and cover fresh concrete with a 6-millimeter plastic sheeting or a spray-on vapor barrier and allow it to cure for seven days.
Altogether, these techniques provide increased wear resistance to manure-scraping equipment. To increase the life of a textured floor, use rubber scrapers. Only experienced concrete finishers should be trusted to texture concrete by this manner.
Alternatively, a textured surface can be cut into existing concrete with a floor-texturing machine. New floors that will be textured after concrete placement and initial curing should be floated with the standard flat-bottom bull float, lightly power troweled and allowed to go through an initial cure (seven days of coverage) before being textured.
Slip and grip
Often the spacing, depth and configuration of deep grooves used in the slip and grip approach favor the concrete finisher or concrete subcontractor charged with creating the grooves rather than benefiting the cows.
Most notably, the grooves are spaced too far apart and result in poor performance as cows’ feet slip, gaining sufficient speed that the foot slips right past grooves, and the cows go down, giving this approach poor marks.
Grooves spaced closer together require more work and effort on the part of the concrete finisher to install, but they limit the distance a cow’s foot slips, if at all, before gaining purchase by the edge of a groove.
Research-based recommendations for grooved concrete floors to provide confident, low-abrasion footing that maximizes the slip and grip method are:
- Groove dimensions: 0.5 inch wide x 0.5 inch deep
- Groove spacing: 2 inches to 2.5 inches on center – this minimizes, perhaps precludes, slippage as cows are likely to almost always have “grip”
- Flat, smooth surface between grooves and a right angle between the floor surface and the vertical sidewall of the 0.5-inch-deep groove
- Orient grooves lateral to the cow’s backbone when possible, as this orientation produce less slip than longitudinal grooves
For flush barns, grooves need to run parallel to the direction of flush when barn alleys are longer than a few hundred feet in length, or less if the volume or delivery rate to the alley of flush water available is limited.
Otherwise, the grooves perpendicular to the direction of water flow will reduce flush water velocity below the amount required to scour and convey bedding and manure to the end of the alley.
Similar to the process of developing a textured floor, wider grooves used in the slip and grip approach can be formed in wet concrete but also cut in after the concrete goes through an initial cure or in older concrete as well.
For the former method, commercially available bronze grooving attachments can be attached to standard bull floats to create grooves in freshly placed concrete. Use many of these grooving attachments on a bull float to create parallel grooves.
Proper moisture content of concrete grooved by a bull float groover makes grooving easier for the bull float operator and results in a quality finished product. Bull floating grooves should be formed after the concrete is placed and screeded but before excess bleed water accumulates on the surface – when normal bull floating should occur.
When concrete is too wet, the bull float is hard to operate because resistance is increased and the grooves tend to fill in with the recently displaced concrete soon after creation.
When the concrete is too dry, the grooving attachments will not fully penetrate the concrete surface, which results in less-than-desirable groove depths, exposed aggregates along the edge of the grooves and a poor finished product.
For the latter method, new concrete floors are grooved after initial curing, or older concrete floors can be re-grooved to enhance traction. In both cases, a saw, similar to one used to cut expansion joints in concrete roadways, can be adapted with a series of diamond dato blades to cut grooves in cured concrete.
Companies that specialize in grooving existing concrete floors generally advertise in popular press dairy magazines and can be found by searching the internet.
Cutting grooves in hardened concrete eliminates the need for contractor experience to groove wet concrete and time-sensitive completion. Concrete slabs-on-grade for use as barn alleys can be placed, screeded, floated and troweled to provide satisfactory results by readily available concrete finishing crews.
However, the additional requirement of installing a specific groove pattern in the slab that is free of rough edges is only successfully accomplished by an experienced crew.
Even experienced crews can fall behind because of erratic delivery of ready-mix concrete to the job site or possibly have unavoidable problems due to changes in ambient air temperature, speed or relative humidity – each and all can affect the outcome, resulting in a poor grooving job.
Diamond and hexagonal patterns can be created in green concrete by using a metal stamp. Usually, the metal stamp is fabricated from round stock material that is cut and meticulously welded together.
The stamp has a metal handle assembly attached, which allows it to be pushed into and removed from the concrete surface while workers are in a standing position. The stamp must be moved several times to fully pattern a barn alley and is generally better suited for small jobs.
Personal experience has shown that stamping concrete is more difficult to accomplish properly than bull float grooving, and stamping is very sensitive to concrete moisture conditions. Concrete that is too wet will stick to the stamp, which causes undesirable rough edges and fins, and results in a sloppy finish.
Concrete that is too dry will bulge up in the inner space between each round stock member used to form the pattern. This concrete bulging results in the floor having several convex areas that do not uniformly support cows’ hooves. Also, when the concrete bulges, it usually cracks on the surface.
The quantity of cracks and their size depends on the moisture content of the concrete at the time the stamp was applied, the design of the stamp and how far it was pushed into the concrete. Surface cracks like this are not desired, as they provide an opening for moisture to penetrate, potentially causing premature floor deterioration due to freeze-thaw action.
At the end of the day, the flooring cows are exposed to should be comfortable enough for humans to walk on barefooted. If you don’t want to walk on the floor because you think it would hurt your feet or be uncomfortable, don’t expect cows to do so.