To read this article in French, click here.
Slurry contains valuable quantities of nitrogen in the form of a liquid: ammonium, usually found in livestock urine. Ammonium is readily available for absorption by plant root systems, but from the moment it hits the barn floor until it is incorporated into the field, large quantities are lost in the atmosphere in the form of ammonia gas. The volatilization of ammonia not only pollutes the environment but also represents a significant cost to farmers who then have to buy expensive fertilizers.
So how do we turn a pollutant into green gold?
How ammonia is formed
The first step is to understand how ammonia is formed: Feces include the enzyme urease, and when it comes in contact with urea contained in urine, it breaks down ammonium into ammonia and carbon dioxide. This process happens during all stages of slurry processing; typically 40% to 50% in housing, 5% to 15% in storage, and 40% to 55% during mixing and land application.
What steps can be taken to reduce this biological process? Frequent scraping at intervals of two hours will prevent the pooling of urine and feces on the barn floor, and cut ammonia emissions inside the barn by 50%. Grooved floors can also channel urine away from the dry matter in between scrapes, helping to create a cleaner environment for livestock.
Prevent losses during storage
The next stage is to prevent losses during storage where urea will be in constant contact with urease and wind will disperse the ammonia. Dry matter in slurry naturally rises to the surface, and as it dries it will create a crust that will reduce emissions by around 40%. Floating covers, such as sheets or plastic spheres, provide immediate coverage and will have 60% effectiveness. Tight, tent-like covers built over concrete or steel tanks provide around 80% effectiveness, while storage bags give even higher protection.
Unfortunately, whichever form of storage cover is chosen, it does not resolve the problem of ammonia emissions. It simply delays the moment when it is released into the atmosphere. Application in the field requires the slurry to be thoroughly mixed into a homogenous liquid that can be pumped and spread evenly for crop take-up. In an open lagoon, a significant amount of ammonia is released once the dry matter crust is broken down by the mechanical action of the agitator and the slurry comes into contact with air.
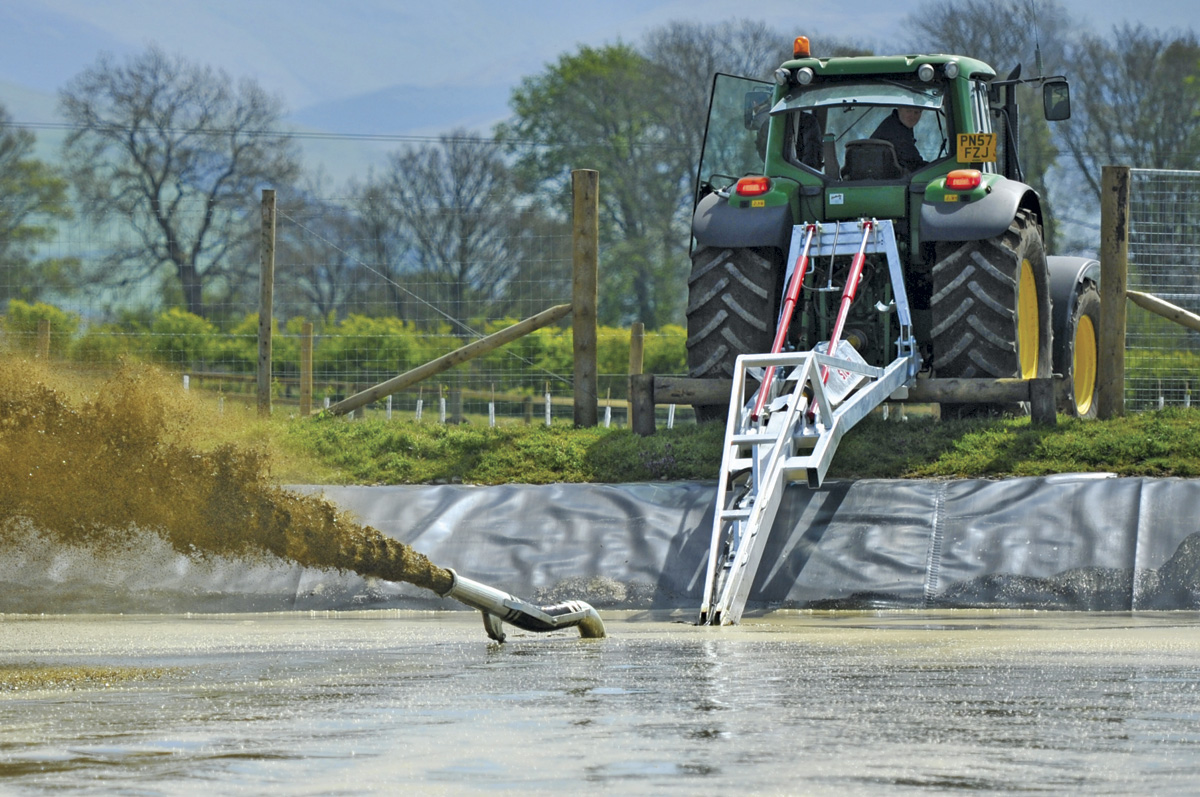
The process of volatilization will continue during spreading, depending on the technique used. Splash plate spreading is economical in terms of equipment, but will maximize the surface area of slurry in contact with the atmosphere, leading up to an 80% loss. Dribble bars and trailing shoes cut down emissions by applying the slurry in narrow bands close to the ground or directly on the soil. The most efficient system uses disc or tine injectors to bury the slurry under the surface.
Prevent formation of ammonia
Is there a way of preventing ammonia formation? As mentioned above, it is the interaction of enzymes and urea which lead to the formation of ammonia. However, this only happens in alkaline conditions, so one solution is to increase slurry acidity.
One way to increase acidity is through the action of aerobic bacteria. These are naturally present in the slurry at ambient temperatures. As part of their life cycle, they digest the slurry and reduce the volume of solids. A useful byproduct of this biological action is a steady increase of acidity. As the slurry becomes increasingly acidic, urease enzymes are inhibited and the breakdown of ammonium is slowed down.
The problem with aerobic bacteria is that they need oxygen to thrive, and slurry is a notably anaerobic environment. The only way to boost the biological action of aerobic bacteria is to reduce the amount of work they have to do and to oxygenate the slurry. To reduce the bacteria’s workload and oxygen demand, a separator can be used to remove dry matter from the slurry. Combined with an aeration system, the bacteria will have enough oxygen to digest the separated slurry.
Aeration systems use low-pressure, high-flow compressors to pump air sequentially through specially designed diffusers laid out at regular intervals on the bottom of storage units, as shown in Figure 1. Each diffuser is connected to a valve block outside the slurry by its own hose, and a ring allows it to be moved into position with a string or a hook. If the diffusers need to be removed, they can be pulled out by hand without emptying the tank.
The air forced through these diffusers comes out as tiny bubbles which slowly rise to the surface. Traditional bubbler systems release large bubbles that rise rapidly and burst on contact with the surface, while smaller bubbles use surface tension to float under the surface and delay the moment they burst. They also have a much greater surface area in contact with the slurry which, when combined with their greater lifetime, leads to greater oxygenation.
A useful side effect of the bubbles is to keep the slurry mixed and prevent the formation of a crust. Not only does this increase the surface area in contact with oxygen, but the slurry is kept homogenous and is available for spreading at any time.
Slurry is often seen as an inconvenient problem for the farm. But a good slurry management plan that encompasses the whole cycle from barn to the field can turn a problem into a valuable resource. With the recent volatility in fertilizer prices and the increasing focus on farming as a source of pollution, proper slurry management is becoming increasingly hard to avoid.