Is labor a challenge? Could you be more consistent with your milking process or milk cows more efficiently? Parlor automation technology decreases labor demands and brings consistency to the milking routine. And you can add many of these solutions to new or existing parlors of any style or brand.
Rotary parlors are growing significantly in popularity to address labor concerns and set farms up for future growth. There are also unique engineering solutions to update parallel parlors with new front-ends to gain the cow comfort advantages and throughput of a new build while using the existing parlor footprint and pit.
One does not need a new facility or a lot of concrete work to take advantage of automation technology in the parlor. Many farms invest in one piece of equipment to partially automate a process and add more in the future. Taking on one new technology at a time helps you focus on that one piece of equipment while not overwhelming the team.
You can expect more consistency from cow to cow with any automation product. But successful implementation is not possible without thoughtful planning, preparation and follow-up.
Weigh your automation options
The most common partial automation parlor technologies replace one or more pre- and post-milking steps. Identify your greatest challenges to pinpoint where you can best streamline your current process.
Some of the most common automation technologies for the parlor are:
Stepover sprayer: A stepover sprayer automatically applies pre- or post-dip in the entrance and exit lanes as cows enter or exit the parlor. Stepover sprayers can work with any parlor configuration, allowing you to use your parlor staff for more critical milking tasks or other management needs rather than just pre- or post-dipping.
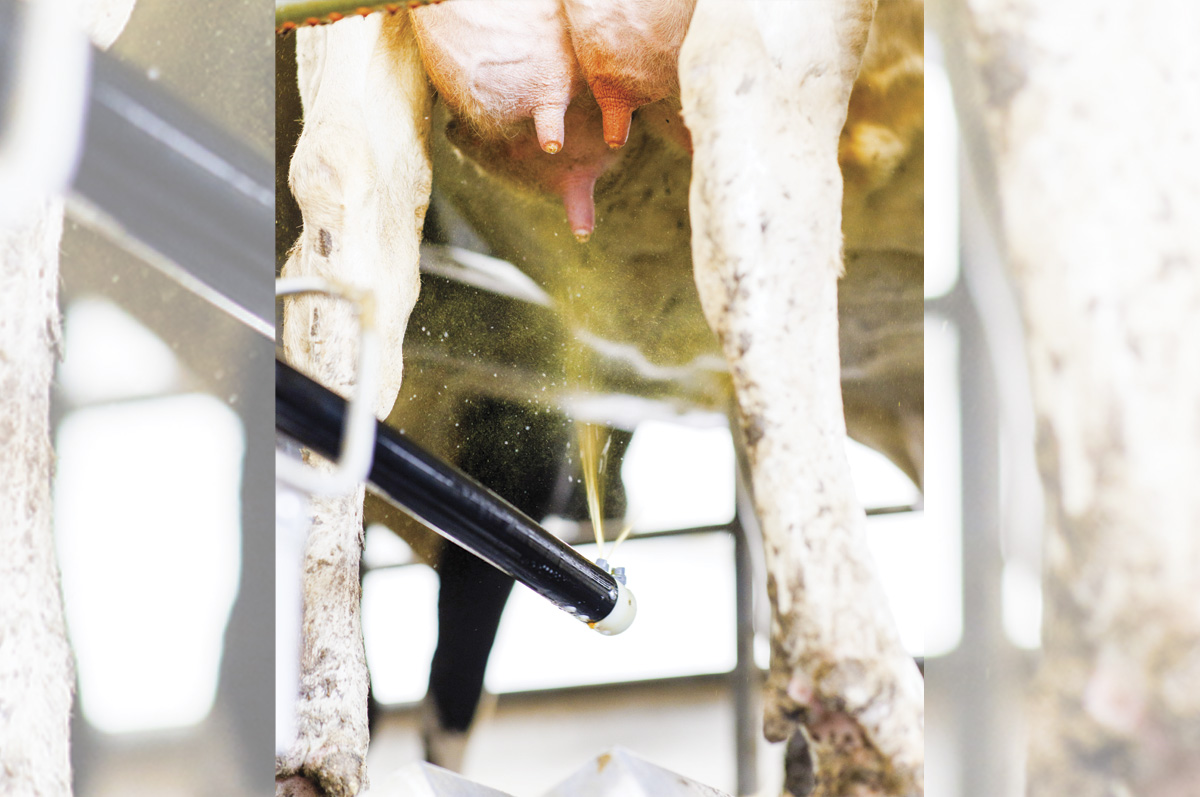
An automated teat dip spray system helps ensure cows are dipped efficiently without slowing down the rotary – reducing the number of people needed on each milking shift. Photo courtesy of GEA.
Teat dip spray arm system: Delegate the pre- or post-dipping task to an automated arm at the entrance or exit of a rotary parlor system. Options today have simple mechanics, do not take up much space and provide a quick return on investment. An automated teat dip spray system helps ensure cows are dipped efficiently without slowing down the rotary – reducing the number of people needed on each milking shift.
Teat prep system: An all-in-one teat scrubber brush system cleans and stimulates teats before milking. These systems require an employee to operate them but can greatly speed up the teat prep process and reduce procedural drift. Dairies can achieve better milk flow rates, maximize parlor throughput and achieve healthier teat ends with the system in place.
Teat stimulation: Automated stimulation (a pulsator upgrade available for some milking systems) has been around for decades, but there is a new wave of interest in this technology. Some dairies that do not want to use a prep brush system use automated stimulation to reduce the amount of manual prep time per cow. Especially in fast-turning rotary parlors, it can greatly speed up the milking process by minimizing prep time while still capitalizing on optimal milk letdown through proper teat stimulation.
Automated detachers: Detachers stop milking at the optimum time, resulting in healthier udders and more efficient milking. Many old detachers are in use today, and since their technology is outdated, they do not work properly and cannot be fine-tuned.
Milk meters: Milk meters connected to herd management software help monitor individual cows and can send signals to the sort gate to get cows into the right management pen automatically. For example, finding cows that drop in milk or are high in milk conductivity could help identify and treat sick cows sooner, something that cannot be done with monthly test data.
Dairies looking to maximize their milking efficiency even further can combine several of these technologies.
What success looks like
Many rotary farms find success in pairing the teat prep scrubber brush on the front end of the parlor with a post-dip spray arm system or stepover sprayer on the back end. One example is a newer rotary parlor installation that milks 60 cows in 8 minutes with three-minute-and-15-second milkouts. Combining the rotary parlor with the automated teat scrubber for cow prep and the automated post-dipping arm fuels efficiency. This farm maintains a 90-pound milk average and 90,000 somatic cell count (SCC) on 2,000 cows.
Another dairy milking in a rotary parlor set a goal to milk 200 to 240 cows per hour with only one person. They achieved this goal by combining an automated teat dip spray arm for pre- and post-dipping with automated teat stimulation. Automated stimulation can be set for 20-, 40-, 60- or 90-second micro pulses, then slows down to begin the normal milking process. It can be preset for each individual cow – for example, 20 to 30 seconds for a fresh cow and 60 to 70 seconds for a late-lactation cow.
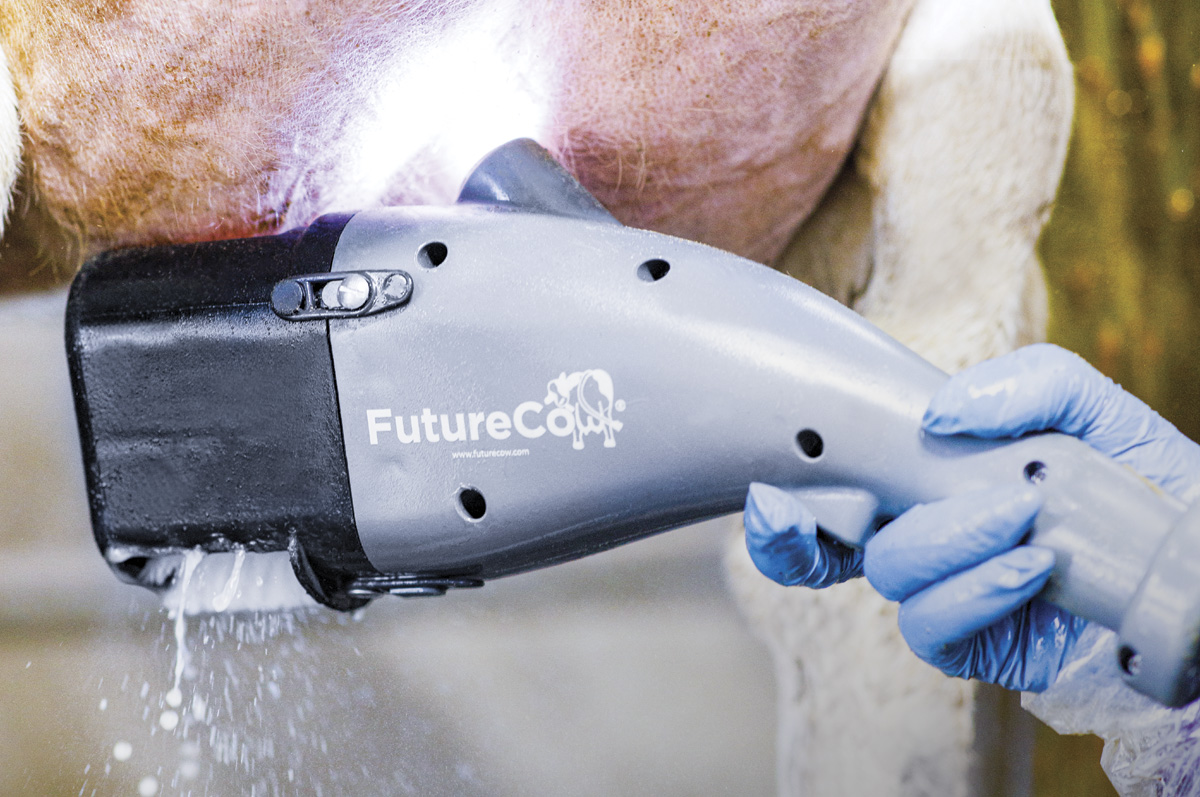
An all-in-one brush system cleans and stimulates teats before milking. These systems require an employee to operate but can greatly speed up the teat prep process and reduce procedural drift. Photo courtesy of GEA.
Considerations before commitment
Teat dip options and cost: The amount of teat dip used by any automated sprayer can be more than manually dipping. Work with your milking equipment dealer and manufacturer from the start so you know the dip volume necessary for effective coverage, and weigh that against the labor savings.
Always ask for a complete list of teat dips you can use in a system, along with the efficacy and cost. Sprayer systems typically have more dip options, while prep brush systems work best with specific solutions. Ensure your dealer partner offers teat dip options with proven, effective killing power across a broad range of mastitis-causing organisms.
Airflow: You may need to adjust ventilation to get better teat dip coverage in spray arm or walkover systems. For example, air blowing into the parlor from fans or overhead doors can inhibit spray accuracy. Closing a door or redirecting fans can help. Adding shrouds on the side of stepover sprayers helps control airflow in the holding area.
Maintenance: Plan for downtime. Just like when an employee calls in sick, having a plan B for that missing labor is imperative. Many farms can perform basic maintenance themselves; others have their dealer do it – it usually depends on their comfort level. If you plan to rely on your dealer during a breakdown or for scheduled maintenance, set expectations with them so you can get back up and running quickly.
Know the maintenance requirements and keep spare parts on hand. Ensure you and your team receive proper training on the equipment so you know what to look for to keep the system operating at peak performance. It can be as simple as keeping an eye on the spray nozzles for the teat dip arm and setting expectations for monitoring them with your employees. For prep systems, maintain a brush replacement schedule and keep extra brushes on hand to help ensure optimal performance.
Having a solid relationship with your dealer and equipment manufacturer can make or break your success when implementing any automation technology. Ensure whomever you purchase from has the expertise for proper milking, disinfecting, prepping and hygiene – and has the resources to support you.