Outstanding Dairy Processing and Manufacturing SustainabilityMilk Specialties Global
With humility and a focus on “doing the right thing,” dairy sustainability has frequently gone under the public radar. Such is the case with Milk Specialties Global (MSG), this year’s recipient of the Outstanding Dairy Processing and Manufacturing Sustainability award.
From its start in 1944, MSG’s founding principle has been creating value from milk’s liquid whey components that cheesemakers and farmers couldn’t sell and that is often considered a waste.
“When we started this company, we had sustainability in mind without knowing it. We’re a recycler of other companies’ byproducts, making high-value material,” says Matt Whann, vice president of sustainability with MSG. “Obviously, as sustainability in the dairy industry has evolved, our customers are asking more of us in terms of sustainability. Within the last couple of years, we’ve started getting serious in terms of how we approach sustainability and how we talk about it.”
While end users won’t see the MSG brand name prominent on product labels, the company is a world leader in the production of whey protein isolate and ingredients. With 11 processing plants, MSG employs more than 1,000 people and produces more than 688 million pounds of product annually. Primary human products are food-grade whey proteins, milk proteins and specialty proteins such as concentrated lactoferrin, marketed under consumer labels sold by major retailers around the globe. Primary animal products are milk replacers for a variety of species and energy supplements for dairy cattle.
The company’s intermediate whey processing facility in Monroe, Wisconsin, is the focal point for MSG’s 2022 sustainability award. The plant addresses two major sustainability challenges while helping grow whey’s nutritional and economic values: Transporting liquids over long distances by truck is highly inefficient and wasteful, and not utilizing every nutrient in milk is also inefficient and wasteful.
The plant is located in Green County, a region rich in dairy farm culture and a major hub of small and medium cheese producers famous for producing award-winning artisan cheeses. But while the area’s rural setting is ideal for dairy farming, it creates logistical challenges for others in the dairy supply chain.
For cheesemakers, entry into whey processing can be cost-prohibitive or simply out of their wheelhouse. Without whey processing capabilities, the leftover whey from the cheesemaking process was trucked out onto farm fields, where it’s land spread or disposed of in other ways.
Partnering for solutions
The solution turned out to be simple on the surface but a challenge to execute. MSG purchased and converted an old cheese plant in Monroe as a staging site, in 2016, seeking to collect whey from the region’s dense cluster of cheesemakers. However, with the local whey supply far outweighing the plant’s capacity, the excess whey would either have to be dumped or moved to the company’s largest whey processing facility, 120 miles away in Fond du Lac, Wisconsin. Rail transport was not feasible. One solution would have been to add more trucks, traffic and transportation costs for hauling a product that contained 90% water.
The MSG project team set out to do the opposite – reduce the number of trucks on the road while also increasing local whey processing capacity, capturing every nutrient in the farmers’ milk and benefiting dairy’s supply chain from farmer to consumer.
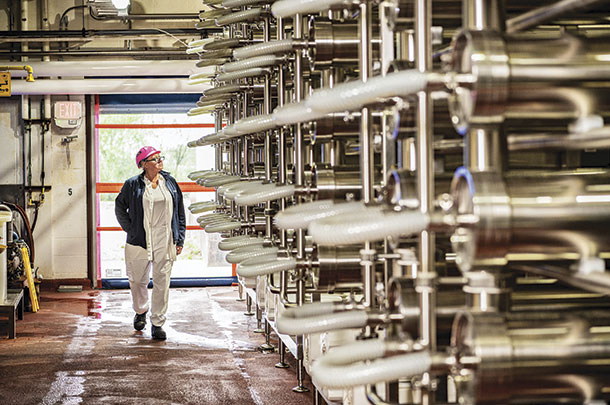
MSG approached Membrane System Specialists Inc. (MSS), an engineering firm specializing in filtration, to design a solution to manage larger volumes of whey without increasing the facility’s footprint. MSS engineers added surface area to the liquid processing equipment and modified the existing filtration system to double the plant’s capacity.
Another key partner was a neighboring business, International Ingredients Corporation, a producer of animal feed products utilizing MSG’s leftover, lower-valued deproteinized whey permeate. The two facilities were connected by a pipeline, and International Ingredients was able to utilize a larger volume of permeate, eliminating the need for additional transportation.
By the numbers
The MSG’s $2.8 million project was fully implemented in late 2021. Through monitoring detailed production records, the metrics tell a conservation and economic success story.
By removing 2.8 million gallons of water annually from whey and recycling it locally, truck traffic from the facility dropped more than 50%, reducing the equivalent of 2,504 heavy trucks passing through the area and cutting traffic by more than 237,000 miles annually. Diesel fuel usage was reduced by 47,446 gallons. Annual company truck expense savings are estimated at $957,616.
The company estimates greenhouse gas (GHG) emissions were cut by 486 metric tons annually, with yearly carbon sequestration equivalent to that from about 595 acres of U.S. forests.
The site’s increased capacity allows MSG to process 20 more truckloads of local whey per day, capturing 377,826 pounds of whey solids from disposal annually and resulting in approximately 53,226 pounds of additional nutritional whey protein isolate to be used in consumer products. That not only creates an additional revenue stream for the small-batch artisan cheesemakers, but the economic benefits are also amplified across the rolling hillsides, supporting local dairy farmers.
Further impacting the local economy and quality of life, the plant added sustainable new jobs and now employs 21 people.
MSG’s culture
The Monroe project has helped drive MSG’s entire culture around sustainability. Through connection to the Innovation Center for U.S. Dairy, MSG sought to align with an industrywide commitment to reach “Net Zero by 2050” goals. Three years ago, the company measured its carbon and GHG footprints for the first time, striving to benchmark efforts “to make sure we’re working on the right things,” Whann says. “We’ve really started to look at sustainability with a more standard lens.”
Reflected in being named recipient of the award, Whann says the sustainability has grown beyond his small team and is company-wide, driven by CEO Dave Lenzmeier’s focus to “do the right thing.”
That energy and emphasis is contagious in the company’s entire workforce. MSG senior marketing manager, Ben Kroeplin, credits some of that to the numerous staff who grew up on dairy farms, with a longstanding appreciation for passing the farm to the next generation, “leaving it in a better place than when you found it.”
“It seems like with every passing year, it becomes a larger conversation; everybody in the company has sustainability goals,” Whann says. “We really try to integrate sustainability into the fabric of what we do.”
While MSG doesn’t have direct contact with consumers, the company has a lot of retail-facing customers who want to talk about sustainability. As a supplier of whey ingredients to those companies, MSG business partnerships have also become sustainability partnerships.
“Customers are really asking for sustainability reports, sustainability progress and sustainability projects. Increased capital is being dedicated to sustainability efforts across the full supply chain,” Whann says.
Kroeplin notes that the company is willing to work not only with customers but also competitors. The technology to concentrate whey solids is readily available, and MSG does not hold any patents on it. Business models may differ, but MSG encourages and supports projects intended to have a positive environmental impact.
“We’re all in this ship together, and we all have to move things forward,” he says. “We might compete for the same customers, but at the end of the day we also think it’s important to look at metrics together and compare notes, how do we make all of us better.”
The Monroe project is one that, in the past, would have received little public notice “because it was the right thing to do,” Whann says. “But when we took a step back and looked at all the impactful metrics on sustainability in that project alone, we’re starting to tout some of the things that are very impactful to sustainability and are good for the dairy industry.”
A model for other locations, companies
MSG publishes an annual Responsibility and Sustainability Report outlining the company’s practices and projects, communicating its efforts to customers, communities and investors. The company is now investing millions of more dollars to replicate some of the Monroe project’s ideas. Preliminary discussions are being held with potential partners exploring strategic locations across Wisconsin. MSG also recently completed a rail expansion project at its facility in Paris, Illinois.
Outstanding Dairy Farm Sustainability
Grayhouse Farms,
Stony Point, North Carolina
Schlangen Dairy,
Albany, Minnesota
Deer Run Dairy LLC,
Kewaunee County, Wisconsin
Bar 20 Dairy,
Kerman, California
Outstanding Supply Chain Collaboration
Bel Brands USA, Land O’Lakes, Inc. and Boadwine Dairy
Outstanding Dairy Processing and Manufacturing Sustainability
Milk Specialties Global,
Monroe, Wisconsin
Outstanding Community Impact