From baling hay to making silage, the performance of your equipment relies on the lubricants used to make it run. Equipment fluids, like engine oil, hydraulic transmission oil, grease and coolants, are the lifeblood of your tractors, self-propelled forage harvesters or mowers and other implements.
Have you established a lubricant and maintenance strategy for your operation? Consideration of the lubricants you use on your machines, plus the maintenance routines you implement, are a primary step toward protecting your equipment to prolong machine life and maximize uptime during hay season, chopping time and winter feedings.
Explore your options
Lubricant choice can directly influence performance in the field. In the past, your choice has probably been based on price, purchasing convenience, quality labels, prior experience or a combination of these factors. Most equipment manufacturers sell and recommend their brand of engine oil, hydraulic transmission oil, coolant and grease, which is known as the genuine or original equipment manufacturer (OEM) choice.
OEM lubricants are designed, tested and approved by the equipment manufacturer and validated through rigorous testing standards and specifications to ensure your equipment performs at its maximum year after year. Selecting non-OEM fluids carries the risk of compromised machine performance, leading to decreased efficiency and productivity. At the end of the day, finding the best lubricant option for your equipment, regardless of age, will be a small investment to protect your large investment on tractors, forage harvesters, self-propelled mowers and implements.
High-horsepower lubricant needs
A tractor uses 90% of its available horsepower when operating in the field, compared to a passenger vehicle only using 30% and semitrucks using 60% of their available horsepower under normal operating conditions. In the hayfield, tractors, especially when operating an implement, or self-propelled equipment operate under stressors and pressures that can impact engine performance. Protecting the engine and transmission moving parts with top-quality OEM lubricants is key to ensure your equipment handles the higher load required to operate at 90% available horsepower.
Factors defining high-quality lubricants
The lubricants flowing through your equipment protect against damage due to wear, corrosion, noise and vibration. Let’s take engine oil as an example. Engine oil mitigates friction and wear on critical components of the machine and provides protection against hotter temperatures and higher pressures, which is especially important with today’s modern high-horsepower engines.
Equipment manufacturers put their engine oil through bench and field testing, completing rigorous in-field activities to ensure OEM lubricants can perform under the toughest conditions. Top-tier engine oils should also provide oxidation resistance to prevent sludge and premature wear within the engine and allow for extended drain intervals to help minimize downtime spent filling and changing engine oil during busy seasons.
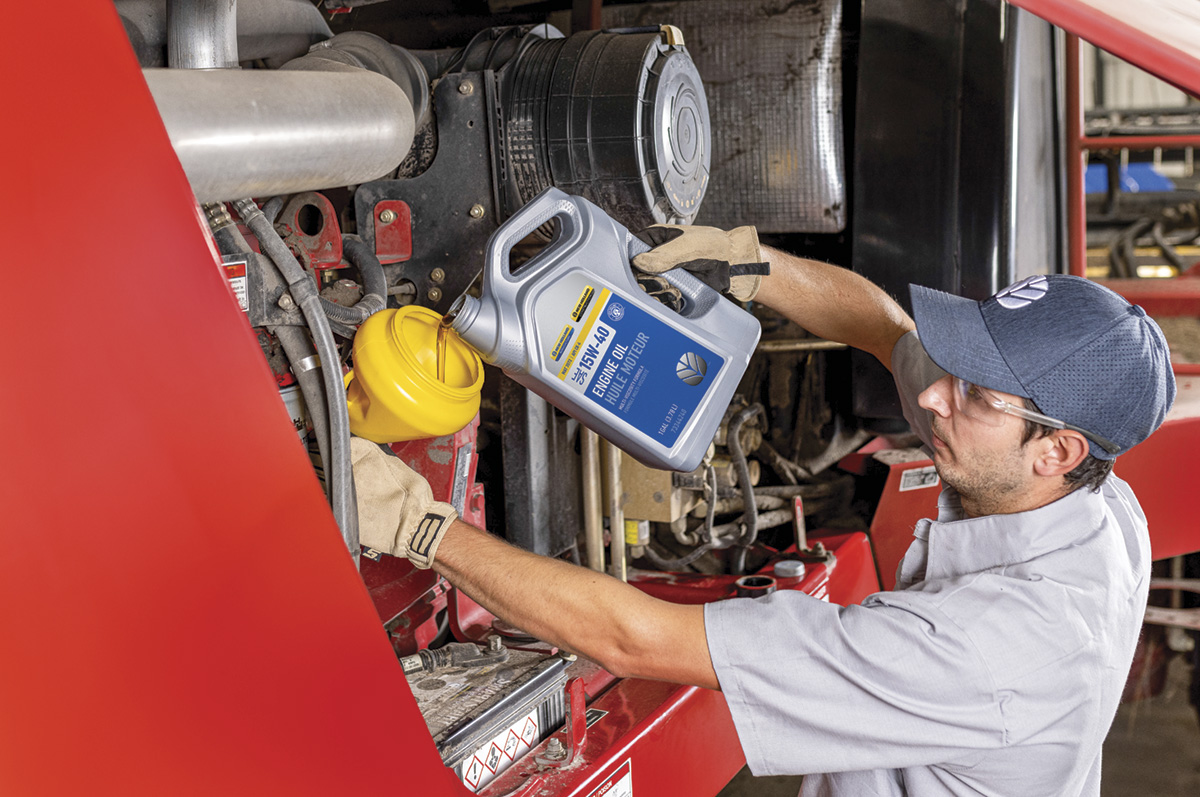
During this time, maintaining your equipment is critical, but operators must also consider what to do with the extra lubricants on hand at the shop. Photo courtesy of New Holland Parts and Service.
Lubricant and maintenance strategies
Establishing a lubricant maintenance strategy for your equipment can help prevent issues that may impact performance and longevity. Your strategy should include the selection of genuine lubricants as well as regular engine oil changes, hydraulic transmission oil and coolant fills, and greasing. Refer to your operator’s manual for your machine’s lubricant specifications, including oil change intervals and grease zerk fitting locations.
Certain steps in your regular maintenance routine should be completed every day during hay and forage harvesting season:
- Greasing to reduce friction, wear and tear on joints, bearings and other necessary parts
- Identifying any broken or worn parts that require immediate attention
- Checking engine oil, hydraulic transmission oil and coolant levels
Gearing up for winter
With hay and harvest season in the rearview mirror and colder weather approaching, now is the perfect time to consider winterization as part of your maintenance strategy. Follow this five-step process to ensure your equipment will come from the shed in prime condition next year:
- Change engine oil: Changing engine oil and filters may be required before the equipment parks for the winter. Used engine oil that settles in your equipment for long periods of time can cause contaminants to impact engine components when started again.
- Fill hydraulic transmission oil: Leaving headspace in hydraulic oil tanks can cause unfavorable liquid formations during cold weather.
- Maintain coolant levels: While coolant helps keep equipment cool in the summer, it also helps prevent freezing in the winter. Be sure your selected coolant is formulated for cold temperatures.
- Keep batteries charged: When equipment is not used and temperatures fall, your batteries may experience a chemical change. Disconnect batteries or use a battery maintainer over the winter.
- Remove dirt and debris: Small pieces of hay, silage or dirt built up on machinery create a prime location for rodents to create nests. Remove debris with an air hose to avoid any issues when starting up equipment next year.
- Repair, replace and upgrade: Downtime during the winter also provides an optimal time to repair and replace broken or worn parts, upgrade technology systems or add new features to your equipment. Complete these repairs in your shop, or schedule time with your local equipment dealer to complete an equipment inspection for a top-down check of your machines to identify maintenance needs.
During this time, maintaining your equipment is critical, but operators must also consider what to do with the extra lubricants on hand at the shop. Be sure to store lubricants in a dry location where the temperature remains moderate, and ensure all containers are well sealed to avoid contamination.
Rely on your equipment dealer
Your local equipment dealer is a go-to resource for your maintenance needs. Some dealerships may provide bulk oil tote storage and convenient delivery options if you use a significant amount of oil for your fleet of equipment, as well as limited-time savings for lubricants, parts and upgrades this winter. Lean on their maintenance expertise, from the resources and knowledge to help you build a maintenance strategy to sourcing the genuine lubricants that fit your equipment lineup.