Dairy producers have a valuable resource in the form of manure to provide home-grown nutrients for sustainable crop production and organic matter back to their soil. However, managing that manure responsibly comes at the cost of cash, labor, and environmental challenges. Manure equipment manufacturers, custom applicators, and dairy farmers have embraced innovation and technology to get the job done well, but will need to continue to evolve to meet the challenges of dairy farming in the Northeast in 2023 and beyond.
In an ideal world, all manure would be applied in a way that maximizes crop nutrient utilization. This optimizes the balance of profitability and reduced environmental risk. However, many challenges keep us from that perfect scenario. Among them are manure storage capacity and location, weather and crop rotations, and equipment limitations. With continued environmental regulations and more intense public scrutiny, dairy producers must continue to improve their manure management. The good news is sound manure management pencils out in the end, as it can equal better soil health, excellent crop production, and reduced fertilizer costs.
Many strategies are available to help manure management be efficient, profitable, and environmentally sound.
DRAGHOSE SYSTEMS AND PIPELINES
The transfer of manure to the field where it needs applied can be the make-or-break part of the profitability equation. With farm fields getting farther away from livestock housing and manure storages, this is particularly true. Pumping is an efficient way to move manure that enables the tractor in the field to maintain productivity without idle time and removes heavy tankers or manure trucks from the road and fields. It reduces fuel use and optimizes labor and equipment. It also creates a public benefit that reduces neighborhood nuisance (and hopefully associated complaints). To maximize pumping efficiency, many farms are now investing in underground manure transfer pipelines. While there is significant upfront investment and challenging logistics, once installed they provide the most efficient way to transfer manure from the storage to the field.
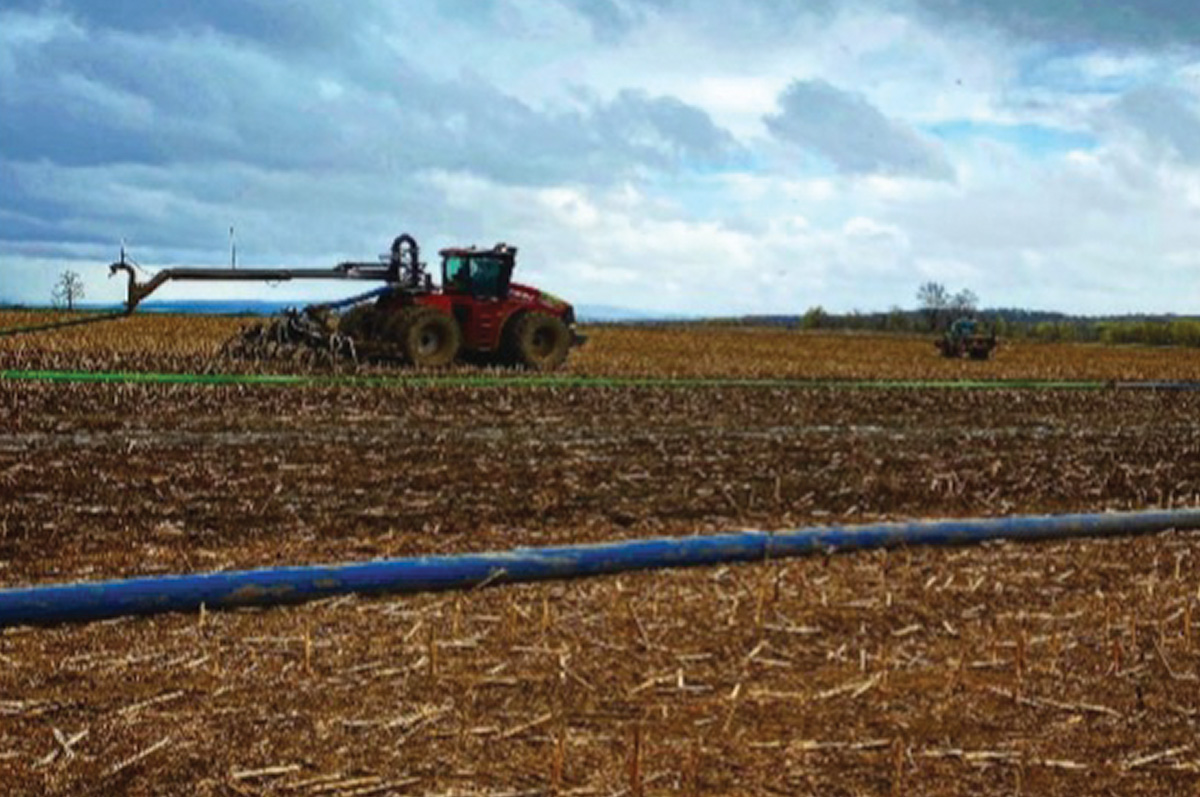
Draghose manure application after corn harvest. Photo by Travis Walton, Walton Manure Management LLC.
Beyond transfer efficiencies, utilization of draghose systems for field application of manure keeps heavy tankers (or worse, trucks) out of fields. Early adopters of this technology are now reaping the rewards of improved soil health thanks to reduced soil compaction. While not perfect for every size farm, even farms with less than 400 cows have been able to adopt this technology with good success given right-sized equipment and a well-trained operator. Satellite manure pits are also an important piece of the puzzle. Locating manure pits near strategic groupings of fields can allow draghose applications to fields farther away from animal housing, thereby distributing nutrients more effectively.
Producers who can’t justify pumping to transfer manure but want to keep heavy equipment off the field, can compromise with use of frac tanks or manure transfer dumpsters to nurse manure to and then pump to the field. Trucks stay on the road and the spreading tractor stays in the field. This allows for high-volume transfers between the storage and field, while the spreading tractor utilizes a draghose for the field application.
Many options are available for producers to find the right fit. If a producer isn’t able to invest in new equipment, many custom manure applicators are equipped and experienced to perform these operations for hire. And, often, they are experts in this kind of application as they have operated the equipment for many years and have upgraded to the newest, safest, and most efficient systems.
INJECTION, DRIBBLE BARS, AND OTHER TOOLBARS
When it comes to maximizing nutrient value of a manure resource, getting it incorporated into the soil as quickly as possible is key. Depending on the state’s nitrogen crediting system for manure applications (and when manure is being spread), inorganic nitrogen credits can be increased anywhere from 40 to 100 percent.
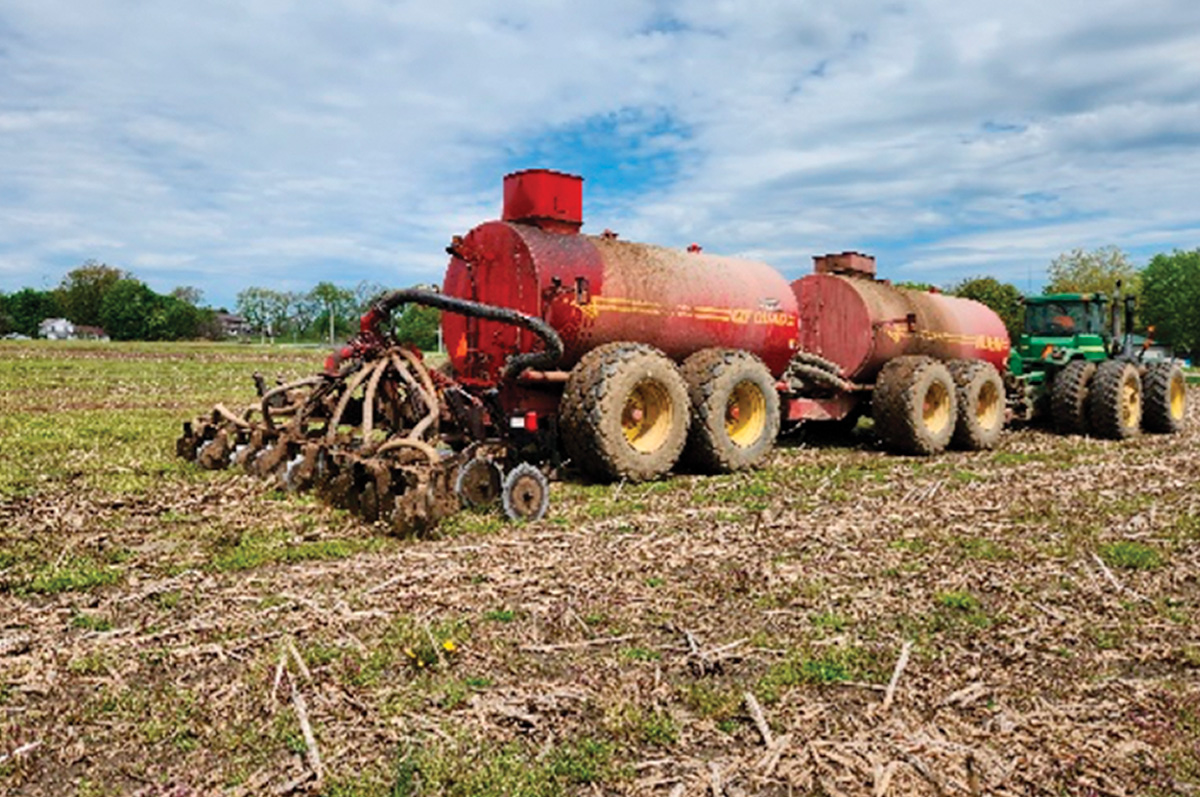
Tank-mounted injector on cover crop. Photo by Juan Carlos Ramos Tanchez, Cornell.
Injection toolbars are now a common piece of equipment and can be modified to fit almost any cropping system, manure application equipment, and manure type. When manure nitrogen is maximized through injection, it is a much more balanced nutrient source that can provide a corn crop the right amount and balance of nitrogen and phosphorus, at a rate of 10,000 to 13,000 gallons per acre. This makes it easier to get manure to more acres and reduces purchased fertilizer inputs. In addition to nitrogen savings, injection reduces the risk of phosphorus loss and thereby allows more flexibility in a Comprehensive Nutrient Management Plan (CNMP) and might open fields to manure applications that were off-limits before.
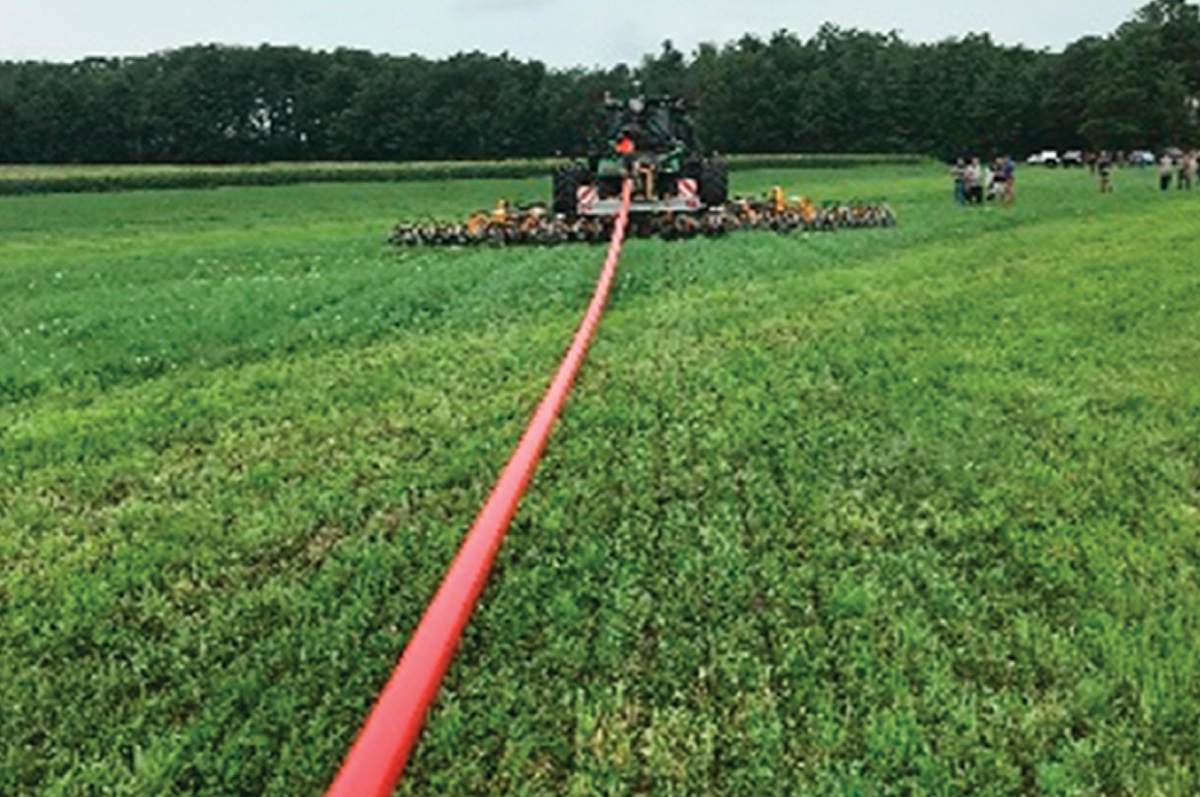
Grassland injector. Photo by Kirsten Workman.
Often, injection equipment can be a bit finicky as we try and move material into smaller and smaller diameter hoses. Injection equipment also has a lot of complexity and maintenance and requires more horsepower to pull shanks and discs through the field. As a result, equipment manufacturers and farmers have started to split the difference with dribble bars. These are simple tool bars that deliver manure through flexible hoses under low pressure right at the soil surface, creating a banding effect.
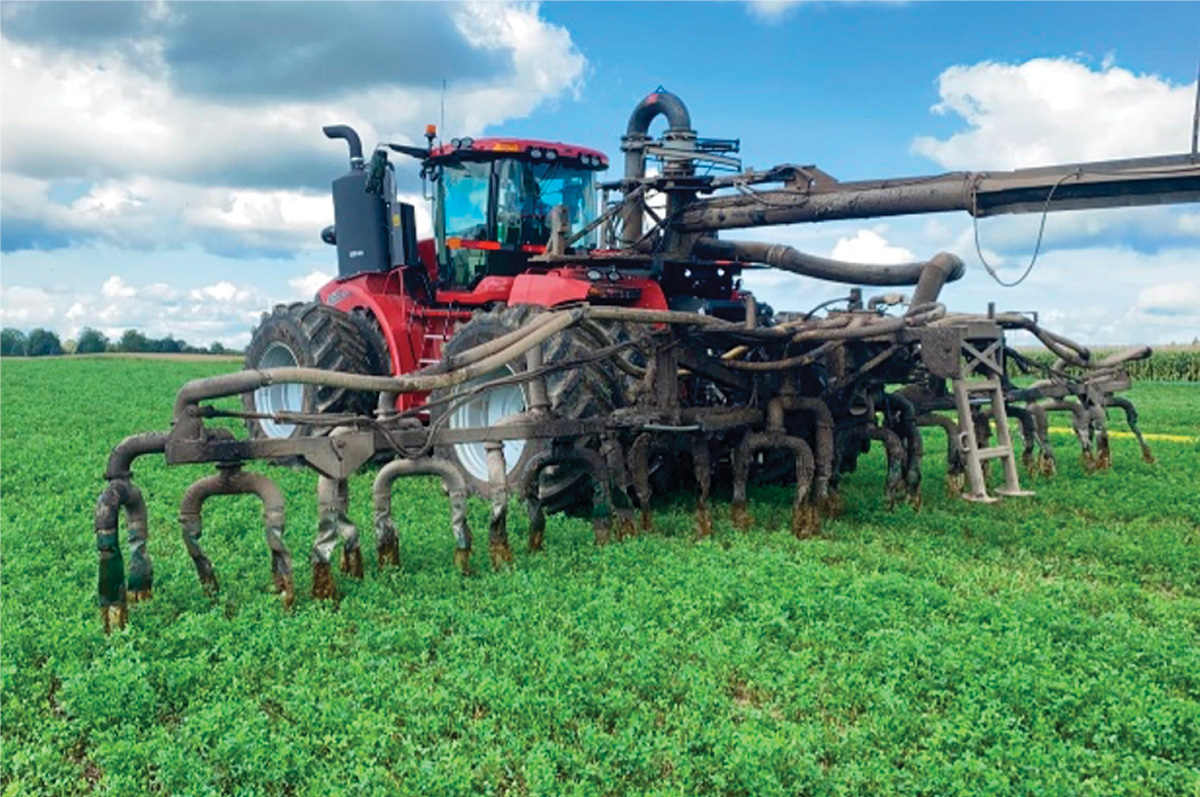
Dribble bar in hay. Photo by Travis Walton, Walton Manure Management LLC.
Dribble bars live between surface applications and injection in terms of nutrient utilization and runoff reductions, but do allow for delivery of manure below the crop in cereal grains, cover crops, hay, and row crops. This equipment has the benefit of a wide range of application rates, reductions in nutrient loss and odor and more uniform application compared to broadcast applications while being faster and requiring less mechanical maintenance and horsepower to injection.
IN-SEASON MANURE APPLICATIONS
In addition to getting manure incorporated into the soil, another way to maximize manure nutrients is to time manure applications as close to (or during) crop growth as possible. While this has been done in hay crops for many years, we are now seeing more applications to row crops after they are emerged. This practice utilizes nutrients more efficiently, gets manure out of storage during the warm summer months when odor and methane emissions can peak, and provides more storage capacity at the end of the season when manure spreading conditions become riskier. Glen Arnold and Ohio State University Extension have done extensive work with swine and dairy manure to demonstrate and troubleshoot in-season applications of manure to field crops. See the Resources section for links to some helpful resources from the OSU team.
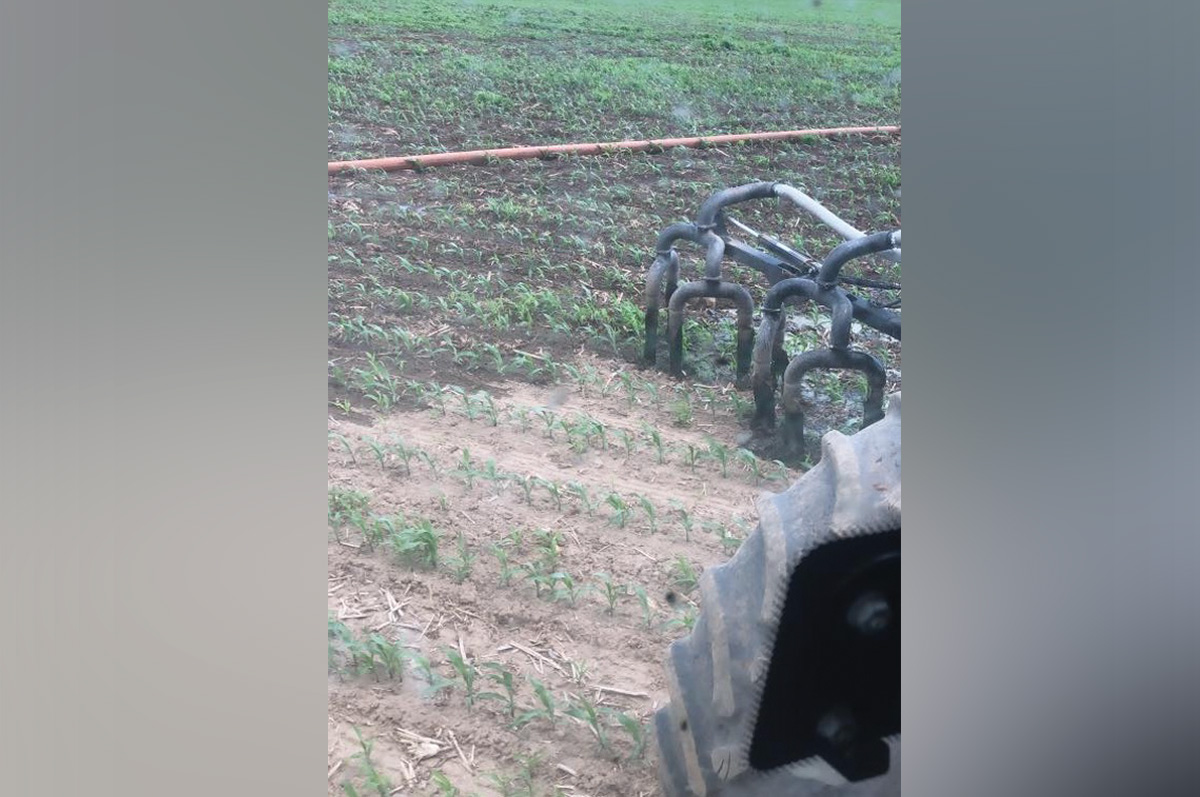
If done early enough, draghose applications on emerged corn can work really well. Here we see a draghose application on V3 corn in western N.Y. using a dribblebar. Photo by Travis Walton, Walton Manure Management LLC.
Corn
Draghose equipment can be pulled over corn up to V4 with moderate surface-application rates around 6,500 gallons per acre. Do not go into fields beyond this point as plants will break off under the tension of the hose being pulled over them. Test fields by stepping on corn plants to see if they snap under your foot. Warmer temperatures also help. Beyond the V3/V4 stage, higher-clearance equipment can be taken through fields and either dribble, drop or inject manure between rows.
Hay/Pasture
In sod crops it is important to avoid getting manure on new growth, degrading forage quality, increasing ash content or creating refusals from livestock. This generally means getting the manure on immediately after harvest and before regrowth. However, with grassland injection equipment or dribble bar applicators, manure can be placed below the sward and in contact with the soil.
Small grains
Winter small grains are excellent places to top-dress fall manure. This increases early crop growth, reduces manure runoff, and these crops utilize nutrients longer into the fall/winter season than even hay and pasture crops. Likewise, manure put on cereal grain crops in the spring while they are still in vegetative growth stages will benefit spring growth if compaction is avoided.
MANURE SENSORS, FLOW METERS, AND GPS TECHNOLOGY
Like all things in agriculture, manure application has new technologies that are being developed quickly. Flow meters and GPS technology have allowed manure to be brought into the precision nutrient management world. Coupled with manure constituent sensing, manure can now be applied by management zone, by targeted rate, and even by targeted nutrient application goals. This allows for efficiency, accurate record-keeping, and the ability to manage better over time. Matched with grid soil sampling and yield monitor data, manure is now part of our precision farming operations.
WHEN TO HIRE OUT MANURE APPLICATION ACTIVITIES
Megan Dresbach of WD Farms LLC does a deep dive on this topic in “Manure application: Considerations for keeping it in-house or hiring out” (agproud.com/articles/57909-manure-application-considerations-for-keeping-it-in-house-or-hiring-out). Key factors that determine which option makes the most sense for an individual farm are whether equipment is available to accomplish the goals for manure applications, whether labor limitations exist in availability or skill level, and on the volume and distance of manure being applied. If hiring a custom applicator means more timely applications or the ability to inject over surface apply, the math can pencil out in a producer’s favor with realized nitrogen savings, labor efficiencies, and ability to utilize equipment that doesn’t need to be owned or maintained by the farm. If custom applicators are tight in the area, this competition with neighbors for services can become a challenge, forcing hard decisions about timing and field conditions in exchange for just getting it done.
RESOURCES
- Draghose application systems for manure
- Manure application cost study
- In-crop application of manure sourced nutrient to maximize crop uptake
- OSU Nutrient Stewardship YouTube channel (videos of in-season manure applications)
![]() |
This article appeared in PRO-DAIRY's The Manager in November 2023. To learn more about Cornell CALS PRO-DAIRY, visit PRO-DAIRY. |