Many calf housing options exist, but important system fundamentals need to be incorporated into the design related to ventilation, calf comfort, labor efficiency, cost effectiveness, and group versus individual housing strategies, for the system to be successful.
Let’s talk ventilation. Calf barns have many sources of contamination: moisture, dust, pathogens, heat, and noxious gases. The goal is to provide fresh air at a sufficient velocity to mix and remove these contaminates without causing a draft on the calves, as well as at a volume such that the exiting air is only slightly stale.
Ventilation is needed not only for the calves but for the barn as well. We want to avoid driving moisture, gases, and pathogens into the structure that could lead to premature failure or serve as a source of future contamination. Except in rare cases, requirements for building ventilation exceeds that for calves.
Required ventilation rates vary with age and size of the calf, season of year, and is measured in cubic feet of air per minute per head (cfm/hd). The second number listed is air changes per hour (ACH). This is the ventilation rate for the building and it is the number of times the entire volume of air in the building is changed each hour. These are target values.
The goal is to accomplish this without creating a draft on the calves. A draft is defined as air with a velocity greater than 60 feet per minute (fpm) and is of greatest concern in the winter. It’s also important to consider these velocities at calf level. We can be standing in the calf barn and feel air moving about our head and shoulders, but this is five to six feet above the floor, and it can be a very different story down in the calf pen. Remember, what counts is what’s happening at calf nose level.
Options for ventilation systems include natural, natural with a mechanical assist, and fully mechanical, including negative, positive or neutral pressure.
NATURAL VENTILATION
Natural ventilation uses the natural forces of wind and thermal buoyancy for the bulk of the ventilation work. As such, the system is less expensive to construct, operate, and maintain. Large openings in the sides and end walls are required, as well as a specifically-sized ridge vent to allow rising air to escape. Because calves produce minimal heat, wind is often a greater factor than thermal buoyancy. Understand, too, this will be a cold facility, usually within 5°F of the outside temperature if there’s no supplemental heat. Occasionally, naturally ventilated barns need some help to facilitate air flow, and this can be done with the addition of circulation fans or positive-pressure tubes.
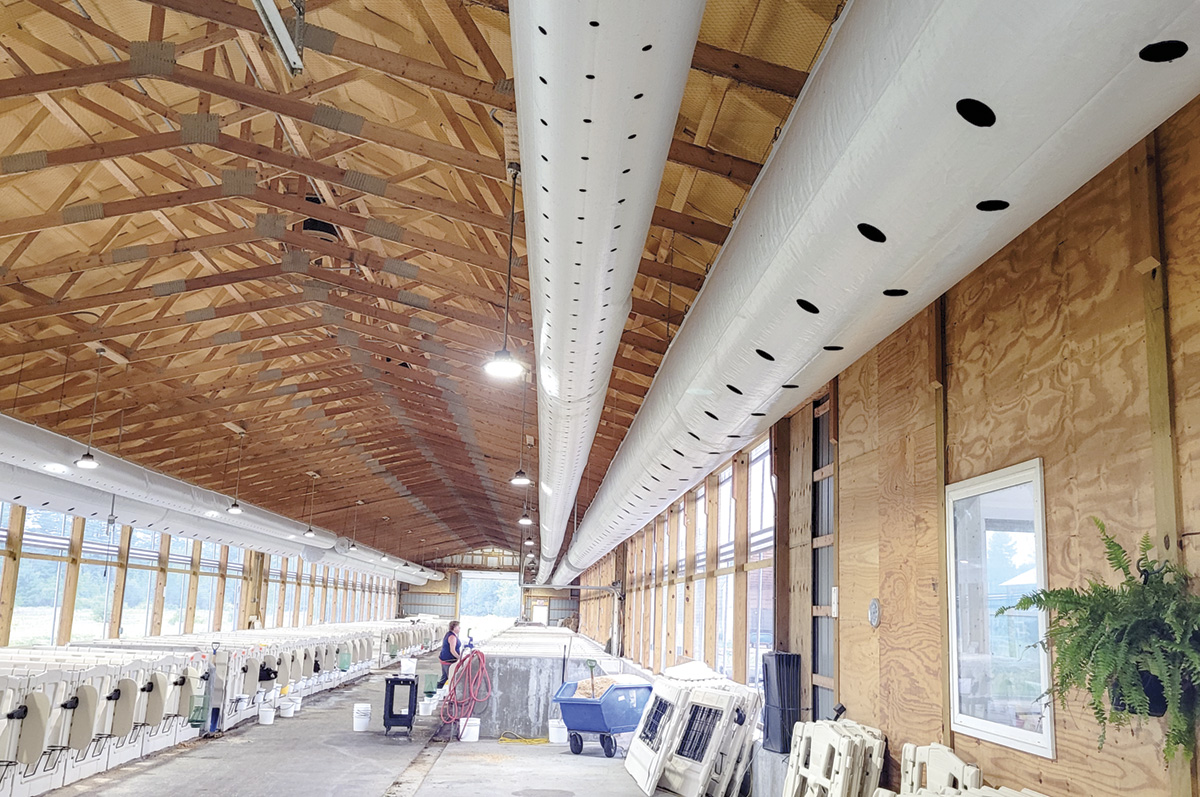
A properly designed positive-pressure tube ventilation system can be a perfect addition to a natural ventilation system. Photo courtesy of Timothy Terry.
The requirements for a natural ventilation system start with good facility site selection. It should have adequate but not excessive exposure – a constant breeze but not a 40-mile-per-hour wind. Due to the potential for airborne pathogens it should not receive exhausted air from a cow facility, and runoff should drain away from, not toward or through, the facility.
The long axis of the building should be oriented perpendicular to the prevailing wind so it’s always blowing through the narrow cross section. Width of the ridge opening should be two inches for every 10 feet of barn width, with eight inches as a minimum. To balance air flow and minimize resistance when the building is closed up, eaves should be open one inch for every 10 feet of barn width.
In most cases, ceiling slope will match roof slope and should be a minimum 3/12, but most are 4/12 or 5/12. Ceiling panels or coverings should be vaulted to the ridge opening or utilize chimneys – one ft2 chimney per 100 ft2 of floor.
More than 50 percent of the side and end walls must be able to open. The addition of split curtains affords the best opportunity to fine-tune air entrance for the season. Usually the top curtain opens down and the lower curtain opens up, often in a one-third to two-thirds ratio. The top opens for good air mixing, especially during the cold, and the bottom opens up to bring in fresh air at calf level. A single roll-up/drop-down unit is easier to automate, and the roll-up feature is easier to maintain as it sheds precipitation and dust.
Barriers to the wind should be absent. Small knolls or hills, adjacent buildings, hedgerows, or tall crop fields can all block natural wind flow through or over the calf barn. Impact of minimum spacing between buildings, or buildings with an obstruction, is a function of the obstruction’s height and its length, and can be calculated: Dmin=0.4(height)(√length).
Open ridges are necessary for wind and thermal buoyancy. Rising air can escape and wind blowing over the opening creates a slight vacuum to help pull air out at the peak.
The open ridge usually needs to have some sort of elevated cap to keep rain and snow out as calves may be housed directly below the ridge opening. In any case, all exposed portions of the structure – trusses, purlins, and gussets – should be covered with aluminum flashing to protect them from the elements.
As the weather warms up, curtains are used to moderate interior temperatures. Moderation of the temperatures is a function of the animals’ thermoneutral range, or the range of temperatures where the animal expends no extra energy to stay warm or stay cool. For newborn calves this range is 50° to 78°F. For calves aged one month or older it extends down to 35° to 78°F.
Recommended curtain position versus ambient temperature is:
- Less than 40°F – ONLY eave and ridge opening, optional supplement of a mechanical system
- 40°to 75°F – variable, depending on temperature, wind, precipitation, and calf population
- Greater than 75°F – completely open
Unfortunately, natural ventilation has limitations:
- Wind tends to enter only on one side so this is problematic in wide buildings (greater than 36 feet)
- Negative pressure assists tend to draw only from the windward side
- Internal barriers such as milk rooms and solid pen panels prevent even distribution of fresh air
- Warmer air from the outside tends to rise above calves, never mixes, and leaves areas of stagnant air
- Still conditions leave dependency on thermal buoyancy, but calves produce minimal heat
MECHANICAL VENTILATION
Mechanical ventilation, however, is an automated system that is not dependent on natural forces. These systems can be negative pressure, positive pressure, or neutral pressure, which is a balanced pairing of the first two. A mechanical ventilation system is required when barns are greater than 36 feet wide, have poor wind exposure, and/or are desired to be operated as a warm barn. Generally, these systems are more automated and complex, and therefore, more expensive to install and maintain. Moreover, managers need to understand how these systems work to effectively manage them.
In a negative-pressure system, fans and inlets cause the air exchange. Fans exhaust air from the barn while specifically designed and strategically placed inlets distribute fresh air. For this system to work, the building must be tightly constructed so that air enters only through the inlets.
A positive-pressure system relies on fans to cause air exchange by forcing air into the barn. Ducts or tubes are used to evenly distribute air. But for fresh air to come in, stale air must leave, so there must be at least two-and-a-half ft2 of openings for every 1,000 ft3 of air coming in. Unlike a negative-pressure system, tight building construction is not required. As long as the minimum opening is met it doesn’t matter where the openings are, which is why this is a great system to retrofit into an older structure.
The fan must be mounted on an outside wall or the end of a duct supplying fresh air. It should never draw air from inside a structure as this will simply redistribute every airborne pathogen in the barn. Moreover, the tube and holes must be specifically matched to the fan to facilitate even distribution along the length and provide fresh air to the calves without creating a draft on the calves.
A positive-pressure tube ventilation (PPTV) system can be a perfect addition to a natural ventilation system, helping to remedy many of the aforementioned limitations. The PPTV system can provide the minimum four ACH consistently. Its uniform distribution ensures no dead spots in the barn or drafts on the calves. As weather warms, the curtains and doors can be opened to provide even more ventilation. In barns with no supplemental PPTV, calves have an almost 81 percent increased likelihood of suffering from a respiratory disease, according to a research report by Jorgensen, et al. in 2017.
In winter, a PPTV system should provide fresh air at a velocity of 50 to 60 feet per minute approximately four feet off the floor. This is considered still, not stagnant, air. In the summer this ramps up to 200 to 250 fpm at one to two feet above the floor. Here it accomplishes two things: 1) ventilation and 2) calf cooling.
At the intake, the fan needs a hood to keep rain, snow, dust, leaves, and litter out of the fan and tube. To do this, it has to have a cross-sectional area of at least two-and-a-half ft2 /1,000 cfm. The hood must be rounded to maintain the same cross-section throughout the air flow. Unfortunately, a simple shed roof hood can restrict air flow and should be avoided.
The holes in the tubes should not all be in the same cross section as this can create a weak area prone to wear or become misshapen under operating conditions. It is better to stagger rows of holes half of the design interval. The tubes also need to be properly supported along their length. A 1/8-inch aircraft cable supported every 20 to 30 feet is usually sufficient. Tubes usually have a grommeted tab that can be clipped to the cable.
If the tubes must be run through the overhead framing because of clearance concerns, protect the tube at all potential points of contact with the framing. This can be done simply with a piece of foam pipe insulation secured to the framing at the point of potential contact.
The fans selected for a PPTV system should be single speed and set with a thermostat. The fluid dynamics within a tube is very fan-specific, and operating more than about five percent outside the design values will result in a poor-performing system. This is another reason that these systems must be designed by a trained professional.
So which system is right for your situation? Follow the decision tree in the “Guidance on evaluating calf barns relative to ventilation needs” fact sheet.
TAKE-HOME
Calf facilities must be designed with the basic needs of the calf in mind. This is nonnegotiable with the builder.
Management is key. Even a well-designed facility can still result in sick calves if not properly managed. However, excellent management can help overcome some design challenges. When it comes to ventilation, hire a professional.
![]() |
This article appeared in PRO-DAIRY's The Manager in July 2023. To learn more about Cornell CALS PRO-DAIRY, visit PRO-DAIRY. |